23 May 2013
Schwafert Torsten: Wieland Is Setting New Digital Standards in Dentistry
Creating an entirely digital dental laboratory
ensures top-precision work at the same high level, and it doesn’t matter at
which point of the globe production is based. New achievements in CAD/CAM
technologies increasingly reassign ever more functions to software and
automation, thus making production of dentures more technology-intensive but
also less difficult. What demand exists in Russian laboratories for recent
achievements in the field, and what innovations Germany-based Wieland is ready
to offer to Russian specialists – we have discussed this all with Schwafert
Torsten, CEO of Wieland Dental.
— What is your estimate of the Russian
market? Is it ready to accept innovative technologies from
Wieland?
— Ever since single-piece restorations became
available, the technology had a huge potential in Russia. I believe that it
will be universally accepted worldwide in future, for multiple reasons. First
of all, patients favor metal-free solutions, because while they are fully
compatible with biotissues and they also have superb esthetic properties. Then
again, they are fairly simple to manufacture, and do not require the use of
sophisticated dental equipment. We offer a rather affordable device that
greatly simplifies manufacturing of such single-piece restorations. By now, 90%
of all dentures in Russia are made of metal, but we believe that the situation
is going to change dramatically in a few years, and then 75% of all dentures
will be monolith, made entirely of zirconium.
— You made a presentation of your TRIOS
intraoral scanner recently. Could you tell us more about the
technology?
— This is an advanced technology indeed, and it’s
becoming available in Russia this year. Intraoral scanning systems gradually
transform the very principle of denture manufacturing. This technology totally
eliminates the standard method that uses imprints and gypsum molds. The time it
takes to make full-zirconium restorations is reduced to just one day. TRIOS
scanning combined with our Mini milling machine and Zenostar materials ensure
uniformly high quality of dental services provided to clients worldwide, and
Russian patients will receive access to the same technology level as those in
Tokyo, New York or Frankfurt.
— Do other companies offer any systems
comparable to TRIOS, or are you the only manufacturer?
— The TRIOS scanner is being produced by our partner
3Shape Company. But you see, many companies make separate products, while
Wieland builds multiple products into a united technological concept.
Therefore, we sell 3Shape products as part of a system. Use of our concept,
plus total compliance of our technology-based production process guarantees a
fairly low manufacturing cost of restorations — some €15 per unit — with
comprehensive ten-years warranty.
— Are you going to bring new products to the
Russian and international markets in 2013?
— We’ll continue our efforts to enable dental science’s
migration to digital technologies and to improve esthetic qualities of our
products. We’re also going to improve our software and hardware, and upgrade
the systems that currently exist.
— There is word that Wieland is going to release
a compact option of its system for cobalt-chromium
milling, and that the system is expected to
be widely used in future.
— We are considering this option at this time.
Cobalt-chromium does have its advantages, and there is a technological
possibility to use it. But marketing-wise, I still believe that the future
belongs to monolith products that are seen today as number one in denture
manufacturing.
— Are you going to make innovative materials in
future?
— Yes, we really are going to focus on them. Wieland
has developed materials and related technologies for over 140 years, and we
continue our work to create materials that enable one-unit milling…
— The ZENOTEC mini device can be described as
your Company’s unique product. How would you comment it?
— Right now, we are focused on improving of our milling
machine that is really easy to use and affordable. Despite its small size,
Zenotec Mini will be quite welcome even in large laboratories that could
install multiple milling machines in the same shop to boost their output. With
Zenotec Mini, you can use materials purchased from any other manufacturers –
it’s a totally open system that we offer.
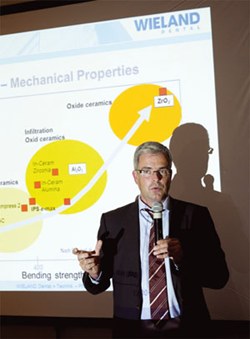
The seminar, Moscow 2012
— Wieland is known worldwide, and the Company’s products are
available in many countries, but where are your sales the highest?
— Export is our strength as we trade with more than
45 countries. The Asian direction has been quite a success as a major
exports market for us. In addition, we perform sales in China, Taiwan, Japan,
Korea, and even some African countries. Incidentally, it’s a fortnight since we
installed our first mini system in Kenya. Here’s evidence that our system can
fit highly different environments. This is why the milling machine that we
mentioned above is our bestseller: it is small, and easily adaptable to any
conditions. We have started sales in Russia only last year, here we cooperate
with UNIDENT, and we hope to sell some 10−15 systems by the year’s end, and a
lot more next year.
— We’d like to learn more about your production
facilities: where are they based, who are the operators, and how it is all
organized.
— Our head office is based in the town of Pforzheim in
South Germany, not far from Schwartzwald – Baden-Baden is the location that
Russians may know as nearest to Pforzheim. Pforzheim is home to our
R&D department, and our office there manages our sales and logistics
processes, and administrative issues. Our factory is not far from Frankfurt,
some 200 km to Pforzheim, and it makes all types of ceramic materials. We also
have a small center elsewhere that mills dental implants used in dentures.
Apart from Germany, our offices also operate in Beijing, in Austria, and the
USA.
Our employees are loyal and enthusiastic, they want their
ideas to drive evolution of dentistry, and this is very important. Wieland has
a history of 140 years, and its current employees combine tradition with
innovation. In the recent five years, work in CAD/CAM technology sector has
become key for us, and we have sold more than 2,000 CAD/CAM systems during the
period.
— They say that your Company has various
corporate programs for employees and clients.
— As is the tradition with many businesses in Germany,
we have a Christmas party for all employees and a large-scale barbecue in
summer. Many of our employees like cycling, and some of them recently went to
Croatia, like our sales department who invite their clients on cycling tours.
An employee of ours is into mountain hiking, and she has arranged a tour
through Latin America for her clients and workmates. Our clients often call us
‘the Wieland family’. We hope that Russia-based specialists will join our
corporate life. Whenever we have an opportunity, we invite specialists to
Pforzheim, we think it is very important, because it is a chance to have a
closer look at our Company. But of course you know that all, and we are glad
that your clients and partners have visited us so many times.
— Now speaking about yourself, how long have you
been with this Company?
— I became the CEO for Wieland three years ago. My
family live near Frankfurt, we have two kids, and my family is very important
for me. My job is time consuming, and besides, I have to travel a lot, so it
doesn’t leave me much time for my family and recreation. Yet I think that I
need to change this all. I use every opportunity to exercise: I play tennis,
ride my mountain bike, and jog.
— My last question is our magazine’s
traditional: What would you wish to our readers?
— We spend lots of time working, and the only way of
having an eventful life is to love your job. I think that dentistry is one of
really interesting businesses, particularly if one considers the changes that
future has in store for us. I sincerely wish that your readers can find and
enjoy the new opportunities.
07 June 2013
The SGS implantation system has been around for a year and a half now on the Russian market. Even if the time is rather short, Swiss-made implants have become available in many clinics over Russia, and so specialists not only are able to get a general impression about the system, but also appreciate the first results of SGS-based reconstructions. Mr. Schabi Michaeli, President of SGS is sharing his impressions about the Company’s operations in Russia.
22 February 2013
Biolase is a manufacturing company that has been a driving force on the market of dental laser equipment for years. The American Company’s products are seen as future that arrives as it presents its every next new development. This time we would like you to meet Dmitriy Butusov, chief R&D engineer of Biolase, and discuss the evolution and problems of laser dentistry.
15 February 2013
Dental Art is known around the world as a manufacturer of the most modern and at the same time exquisite furniture for dental clinics. The company creates not only unique design solutions, but also a space arrangement phylosophy in general. The Dental Art's phylosophical system always brings to the fore the doctors and doctors' everyday tasks, to solve which Dental Art involves innovation technologies. We discussed the process of creating unique furniture with John Fachchin, the company's Director for Exports.
25 October 2012
UNIDENT has always presented a wide range of Premier products on its dental exhibition stand.
Vital dental materials can be found under the U.S. brand. The company has moved to the market its brand new products recently which the professionals found quite interesting.
03 October 2012
Dental equipment and materials under the Italian brand Zhermack can be seen on the stand of UNIDENT at any exhibition. All throughout the Dental Salon, Nicola De Rossi (Product Manager) with the zeal of a true Italian held master classes on dental laboratory equipment.
Back